Construction Containers: An Innovative Solution for Modern Building Pr…

In the ever-evolving landscape of construction, innovation is key to staying competitive and meeting the demands of modern building projects. One of the most significant advancements in recent years is the use of construction containers. These versatile and durable structures have transformed the industry, offering a range of benefits from cost efficiency to environmental sustainability. This article delves into the world of construction containers, exploring their types, applications, advantages, and addressing common FAQs.
What Are Construction Containers?
Construction containers, also known as shipping containers or modular containers, are large, standardized steel boxes originally designed for transporting cargo by sea, rail, and road. However, their robust design and modular nature have made them an attractive option for various construction applications. These containers can be repurposed and modified to serve as temporary or permanent structures, including offices, storage units, living spaces, and even entire buildings.
Types of Construction Containers
New Construction Containers
- Standard New Containers: These are brand-new containers directly from the manufacturer, typically used for high-demand projects requiring pristine conditions.
- Customized New Containers: These containers are tailored to specific project needs, with modifications for windows, doors, insulation, and other features.
Used Construction Containers
- One-Trip Containers: These containers have been used only once for shipping and are often in excellent condition, making them a cost-effective choice.
- Reconditioned Containers: These are used containers that have been repaired and refurbished to meet specific standards.
Modular Construction Containers
- Prefabricated Modules: These containers are designed and built in a factory, then transported to the construction site for assembly.
- Custom Modules: These are modified on-site to fit specific project requirements, offering flexibility and customization.
Applications of Construction Containers
Construction containers are used in a variety of applications, each tailored to the unique needs of a project. Here are some of the most common uses:
Temporary Construction Offices
- On-Site Management: Construction companies use containers as offices for project managers, engineers, and other staff.
- Meeting Spaces: Containers can be converted into meeting rooms, training areas, and break rooms.
Storage Units
- Material Storage: Containers are ideal for storing building materials, tools, and equipment.
- Document Storage: They can also be used to securely store project documents and records.
Modular Building Units
- Residential Units: Containers can be transformed into living spaces, from single rooms to multi-story apartment complexes.
- Commercial Buildings: They are used to construct retail spaces, office buildings, and warehouses.
- Emergency Housing: In disaster-prone areas, containers can be quickly deployed to provide temporary housing.
Construction Site Amenities
- Toilets and Showers: Containers can be fitted with plumbing and electrical systems to serve as hygiene facilities.
- Kitchens and Dining Areas: They can be converted into fully functional kitchens and dining spaces for workers.
Advantages of Using Construction Containers
The use of construction containers offers numerous advantages over traditional building methods. Here are some of the most significant benefits:
Cost Efficiency
- Lower Material Costs: Containers are often less expensive than traditional building materials.
- Reduced Labor Costs: Prefabricated and modular containers require less on-site construction, reducing labor expenses.
- Faster Installation: Containers can be installed quickly, minimizing project delays and additional costs.
Environmental Sustainability
- Recycling: Using containers is a form of recycling, reducing the environmental impact of new construction.
- Energy Efficiency: Containers can be insulated and equipped with energy-efficient systems, lowering operational costs.
- Reduced Waste: Modular construction minimizes construction waste, as components are built in a controlled factory environment.
Flexibility and Adaptability
- Customizable: Containers can be modified to meet specific project requirements, from adding windows and doors to installing complex electrical systems.
- Mobile: They can be easily transported and re-used on different sites, making them ideal for temporary projects.
- Quick Deployment: Containers can be delivered and set up faster than traditional construction, allowing for rapid response to project needs.
Safety and Security
- Structural Integrity: Containers are built to withstand harsh conditions during transportation, making them extremely durable.
- Security Features: They can be equipped with locks, alarms, and other security measures to protect valuable materials and equipment.
- Fire Resistance: With proper modifications, containers can be made fire-resistant, adding an extra layer of safety.
Space Utilization
- Compact Design: Containers are compact and can be stacked, maximizing space on small construction sites.
- Multi-Functional: They can serve multiple purposes, from storage to living spaces, optimizing resource use.
Common FAQs About Construction Containers
Are construction containers safe to use?
- Yes, construction containers are designed to be extremely durable and can withstand harsh environmental conditions. They can be modified to meet safety standards, including fire resistance and structural integrity.
How long do construction containers last?
- High-quality construction containers can last for decades with proper maintenance. New and one-trip containers tend to have a longer lifespan than reconditioned ones.
Can construction containers be customized?
- Absolutely. Construction containers can be customized with windows, doors, insulation, plumbing, and electrical systems to meet the specific needs of a project.
Are construction containers environmentally friendly?
- Yes, using construction containers is a form of recycling, reducing the need for new materials and minimizing waste. They can also be equipped with energy-efficient systems to lower environmental impact during use.
How are construction containers transported?
- Construction containers can be transported by truck, rail, or sea. They are designed to be stackable and can be moved using cranes and forklifts.
What are the regulations for using construction containers?
- Regulations vary by country and region. It is important to consult local building codes and obtain the necessary permits for using construction containers. Some areas may have specific requirements for modifications and installations.
Can construction containers be used for permanent structures?
- Yes, construction containers can be used for permanent structures. They are often used in the construction of residential and commercial buildings, providing a cost-effective and sustainable alternative to traditional methods.
Steps to Implement Construction Containers in a Project
Assess Project Needs
- Determine the specific requirements for your project, including the number of containers needed, their intended use, and any necessary modifications.
Source Containers
- Research and select a reputable supplier. Consider the condition, size, and cost of the containers.
Design and Modification
- Work with a design team to create a layout that meets your project needs. This may include adding windows, doors, insulation, and other features.
Obtain Permits
- Consult local building codes and obtain the necessary permits for using and modifying construction containers.
Transportation
- Arrange for the transportation of containers to the construction site. Ensure that the site is prepared for their arrival and installation.
Installation
- Set up the containers according to the design plan. This may involve stacking, securing, and connecting multiple units.
Final Inspection
- Conduct a final inspection to ensure that all modifications meet safety and quality standards. Address any issues before using the containers.
Construction containers have revolutionized the building industry, offering a cost-effective, sustainable, and flexible solution for a wide range of projects. From temporary offices to permanent residential units, these versatile structures are proving to be a valuable asset for construction companies and developers alike. By understanding the types, applications, and advantages of construction containers, stakeholders can make informed decisions and leverage this innovative technology to meet their project goals.
Additional Resources
- Construction Container Suppliers: A list of reputable suppliers and their contact information.
- Design and Modification Services: Companies that specialize in customizing construction containers to meet specific project needs.
- Building Codes and Regulations: Links to local and national building codes relevant to the use of construction containers.
By embracing the potential of construction containers, the future of building projects looks both brighter and more sustainable.
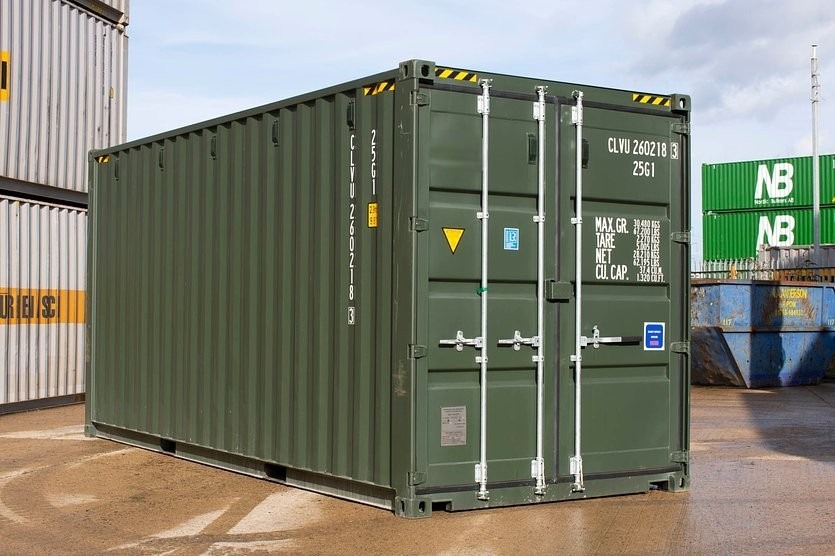